Colecovision Custom Controller
Arcade Parts
How the Original Colecovision Controller Works
Before i start the explanation of how the arcade parts work, its a good idea to start with a basic understanding of how the original controller works first. Fortunately for us, the colecovision controller is a pretty simple device.
Fire Buttons
The fire buttons and the directional joystick on your original colecovision controller are essentially just switches. When you press one of the fire buttons on your controller, you are closing a circuit and allowing a small current to flow through the button, back to the colecovision console. The colecovision receives the signal and depending on which game you are playing, your character will respond by jumping or shooting etc.
Directional Joystick
The direction joystick is made up of 4 switches, one for each direction, up, down, left, and right. when you hold the joystick in a particular direction, you are sending a signal to the colecovision to tell it to move your character in that direction. If you push the colecovision joystick in a diagonal direction, lets say up and left, you are closing 2 circuits, one for up and one for left. Your character on screen will move accordingly. The colecovision will continue to receive these signals until you let go of the joystick or change direction.
Using Arcade Parts For your Custom Controller
In my design I have used arcade parts for the controls. The idea came to me when I first took apart an original controller and noticed that the original controllers inner workings were very similiar to how arcade parts function.
Arcade Buttons
All arcade buttons and joysticks use "microswitches". These are switches that can be wired up in a variety of ways depending on the application. For our purposes, we only need to use them in a: off when depressed / on when pressed manner (as described above).
You will have 2 wires connecting the interface board to each arcade button. To wire the microswitch so that it behaves as we want it, you connect one of the 2 wires to COM (otherwise known as 'common' or 'ground') and the other to NO (normally open). This means that the circuit is open, until the button is pressed. When the button is pressed the circuit closes and a signal is sent to the colecovision. You can connect either wire to either terminal as they are not polarised. NC stands for 'Normally Closed'. This terminal is not used for our purposes.
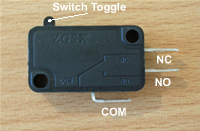
The terminals of a microswitch
Click to Enlarge
Note: To get a better understanding of how the microswitch works, view the enlarged version of the above picture. You can see on the casing of the microswitch how the switch works internally. When the button is pushed down the lever inside changes from NC to NO.
The following picture is an example of a button with a microswitch wired up in this manor.
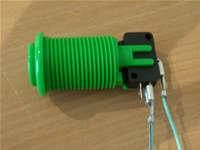
Pushbutton wired for use with a Custom Colecovision Project
Click to Enlarge
The pushbuttons I have used for my project are like these.They require a 28mm hole in the top of your project enclosure. To cut out such a hole, use a drill bit know as a 'Spade bit'. These bits are common for drilling large holes in wood and can be found at most hardware stores. They can be used in either a hand drill or a drill press. You should also check your enclosures top panel thickness to make sure your buttons will fit correctly.
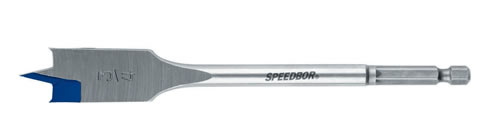
Spade Drill Bit
Arcade Joystick
An arcade joystick has 4 internal microswitches, one for each direction. Unfortunately the microswitches / directions are not usually layed out in an obvious configuration. If you use spade connectors for your internal wiring (discussed below) you can easily plug all the connectors into the joystick and test the directions. Then switch off the console and re-assign each of the cable pairs to the right microswitch. This is the easiest way i have found to wire up a joystick.
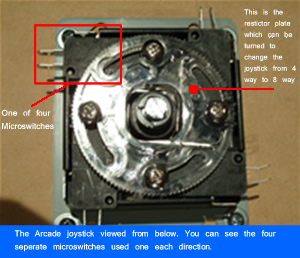
Joystick Microswitches
Click to Enlarge
The Joystick that i have used for my project is a Sanwa like this one. These can be changed from 4 way mode to 8 way mode (see above photo) by loosening the 4 screws securing the restrictor plate and turning the restrictor plate. The Joystick shaft requires a hole of 20mm. However Instead of buying 2 seperate spade bits (one for pushbuttons and one for the joystick shaft), you can use the 28mm spade bit for the joystick to save buying another spade bit just for the one hole. The dust cover on the joystick is quite large and will cover the extra width of the opening:
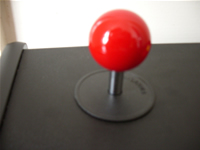
Joystick Dust Cover, Covering shaft hole
Joystick Types
Most joysticks are similiar, varying only in quality and action. The spring tension from one joystick to another can vary as some have a short throw, where as others have a longer movement. Sanwa joysticks like the one that I have used have a light spring pressure for really fast movements. They are also available with balltop or baton shaped handles.
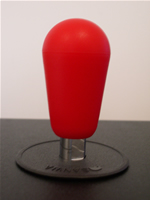
Spade Connectors
I higly recommend the use of spade connectors to hook up your pcb to the pushbuttons / joystick. These fit snugly onto the terminals and can be disconnected effortlessly when required, instead of soldering cables on and off which can get messy and tiresome.
The spade connectors i used for my controller are 7mm in size. You dont have to use spade connectors that are the exact size of the terminals (they can be bigger), but the closer they are, the tighter the fit.
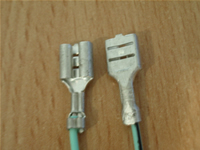
7mm Spade Connector
How to install a pushbutton and microswitch into an enclosure
Even though the process of installing a button into an enclosure is pretty straight forward, this information could be useful for people that are in the planning stages of there controller and also for those that have never done this before.
1) In the top of your controller enclosure with the microswitch removed (otherwise it will not fit), fully Insert Pushbutton into pre-drilled hole.
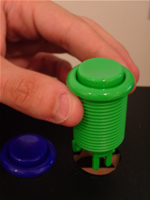
Click to Enlarge
2) On the underside of controller enclosure, screw the large plastic ring / nut that comes with the pushbutton to fasten the button firmly to the enclosure
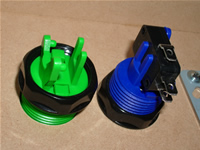
Click to Enlarge
3. Insert the microswitch diagonially onto the pivot notch of the pushbutton (you can see both notchs clearly in the above photo).
You can not insert a microswitch, unforcefully, the wrong way around. If its in the right orientation it will fully insert into the pushbutton harness
Click to Enlarge
4. Lower the microswitch onto the final notch so that it locks into place.
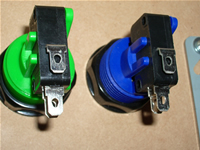
Click to Enlarge
Onto Next Secion
|